The Unexpected Challenges of Using Nylon Strings on Electric Guitars A Sound Engineer's Perspective
The Unexpected Challenges of Using Nylon Strings on Electric Guitars A Sound Engineer's Perspective - The Tension Conundrum Intonation Issues and Structural Concerns
The inherent lower tension of nylon strings compared to their steel counterparts creates a complex interplay of issues when used on electric guitars. This reduced tension can manifest as unwanted buzzing or inaccurate pitches, particularly when the instrument is not optimally set up. Intonation problems, often linked to the bridge saddle's positioning, can be amplified with nylon strings. A slight forward or backward tilt of the saddle can exaggerate these tuning difficulties, requiring adjustments to achieve the desired pitch. Some players attempt to mitigate these intonation inconsistencies by adjusting their tuning strategy, opting to tune to the fifth fret instead of the open string in a bid to even out tuning irregularities across the fretboard. However, these are band-aid solutions at best. The compatibility of nylon strings with typical electric guitar setups is also a concern, especially those relying on magnetic pickups. The weaker signal produced by nylon strings can cause these pickups to fail in accurately capturing their nuances, leading to a less than satisfactory audio output. Ultimately, utilizing nylon strings on an electric guitar necessitates a more nuanced approach to the instrument's setup and playing style. While these strings undoubtedly offer a unique sonic palette, their successful integration requires careful consideration of the technical challenges they present.
The reduced tension inherent in nylon strings, compared to the standard steel strings, presents a unique set of challenges regarding intonation on electric guitars. Especially when venturing beyond standard tunings, the lower tensile strength can lead to inconsistent and difficult-to-predict pitch variations. This is exacerbated by the fact that the bridge saddle, a crucial element in string alignment, becomes more sensitive to shifts. Minor tilts can easily amplify intonation discrepancies, making tuning a delicate process. Some players have adopted strategies like tuning to the fifth fret instead of the open string to try and average out these inconsistencies. This approach, while a practical workaround, doesn't eliminate the underlying problem.
Beyond intonation, the differing material properties between nylon and steel significantly alter how sound waves interact within the guitar body. The less rigid nature of nylon influences the resonance characteristics, often resulting in a less robust and potentially muffled tone. This may not be ideal across all musical genres, requiring careful consideration of the tonal palette desired. This altered resonance also plays a role in how magnetic pickups respond. The different frequency response of nylon strings can lead to a unique harmonic signature, often producing a warmer, softer sound. While some might find this appealing, sound engineers accustomed to the clearer, brighter tone of steel strings may encounter difficulties achieving their desired sonic goals. This disparity highlights the need for adapting mixing techniques to manage these altered sonic properties.
Furthermore, the inherent flexibility and sensitivity of nylon to external factors like temperature and humidity creates another layer of complexity for sound engineers. Environmental changes directly affect nylon's physical properties and can lead to unpredictable fluctuations in pitch and tone. Maintaining consistent sound quality requires careful attention to climate control and potentially, frequent retuning during recording sessions.
The combination of these factors creates a scenario where using nylon strings on an electric guitar transforms the instrument's overall sound and playing experience, thus challenging conventional recording approaches. It adds an extra layer of complexity for capturing the intended sonic outcome in audio productions, whether it be for voice cloning, podcasts, or traditional music recording. It demands a heightened level of attention to microphone placement and audio signal processing to properly manage these nuances. The soft feel of nylon also changes the feel and dynamics of playing, impacting how musical expression translates to the final recording.
While this unconventional approach certainly offers an intriguing palette of sounds for exploration and experimentation, it undeniably requires a greater understanding of how these variables impact the final recording.
The Unexpected Challenges of Using Nylon Strings on Electric Guitars A Sound Engineer's Perspective - Buzzing and Pitch Problems With Lower String Tension
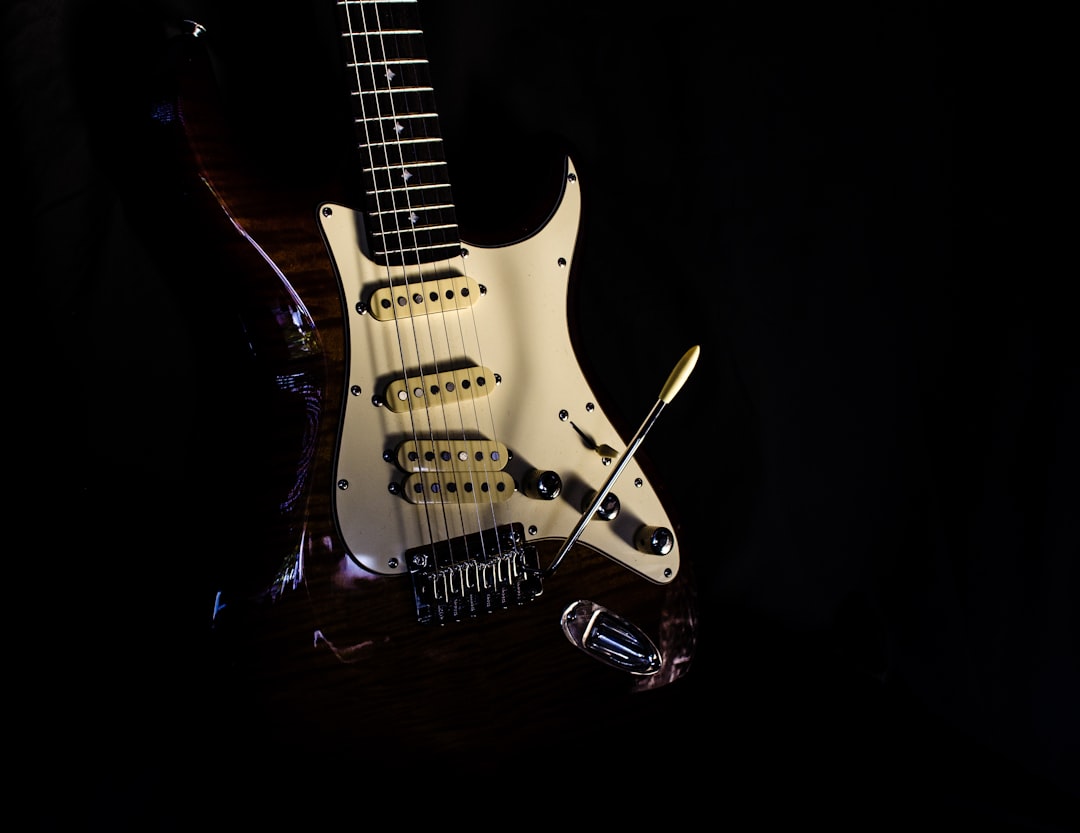
Nylon strings, due to their inherently lower tension compared to steel strings, can introduce a set of audio challenges when used on electric guitars. One of the most noticeable problems is buzzing, often caused by the strings being too close to the frets, particularly if the nut slots are poorly cut or worn. This can lead to an unwanted, noisy sound during playing.
Additionally, the reduced tension can impact intonation, making it more sensitive to changes in the bridge saddle's position. Even slight adjustments can lead to noticeable pitch discrepancies, making tuning a more intricate process. Furthermore, the softer response of nylon strings can sometimes lead to a less robust interaction with magnetic pickups. This may result in a weaker signal and a less pronounced sonic character, posing a potential hurdle for sound engineers seeking a specific tone.
Ultimately, using nylon strings on an electric guitar requires a more thoughtful approach to both setup and recording. Understanding how these lower-tension strings interact with the instrument and its pickups is crucial for achieving the desired sound in a recording environment, whether it's for voice cloning projects, podcast production, or traditional audio recordings. The subtle yet distinct tonal shifts that arise require a more careful consideration of microphone placement and audio signal processing during the production process.
The reduced tension inherent in nylon strings, when compared to steel, introduces a unique set of sonic challenges, particularly when used on electric guitars. One notable issue is the tendency for increased buzzing, especially in higher frequency ranges. This can result in unwanted 'fizz' during recording, which can be tricky to remove during post-production. The lower tension also impacts the player's ability to control dynamics. Soft playing might lack volume and clarity, while harder playing can exacerbate buzzing, creating difficulties for mixing, especially in genres requiring controlled dynamic ranges.
Beyond these issues, nylon strings demonstrate a greater degree of pitch variation, not only across the fretboard but also within individual notes over time. This inherent instability presents challenges for pitch correction software, making achieving consistent pitch more difficult. The unique harmonic signature produced by nylon strings can interact unexpectedly with microphones and recording equipment. Achieving a balanced sound becomes a more nuanced process as unwanted resonance may overshadow the intended tonal qualities.
Capturing the desired sound with nylon strings often requires experimentation with recording techniques. Engineers frequently explore different microphone placements and types to mitigate inherent challenges in achieving clarity and detail. Nylon's sensitivity to humidity is a significant factor, as fluctuations in moisture levels can affect string tension and tone during recording sessions. This necessitates meticulous climate control during the recording process to ensure consistency.
Magnetic pickups, typically optimized for steel strings, struggle to capture the weaker signal produced by nylon strings. This can lead to a loss of clarity and detail in the captured audio, possibly requiring specialized pickups or preamplification. Analyzing the frequency response of nylon is also crucial for engineers. They often find the overall output skewed towards lower frequencies, necessitating adjustments during mixing to achieve balance.
The use of nylon strings might necessitate new approaches to intonation calibration. Traditional setups designed for steel strings may need adjustments to the nut or saddle height to optimize intonation and overall sound production. The distinct playing feel provided by nylon also influences how players execute musical phrasing and dynamics. This altered playing style can translate to unique textures in the recordings, requiring a mindful approach to capturing the artist's intent accurately.
While these challenges exist, they underscore the unique sonic characteristics of nylon strings. Their implementation introduces a novel sonic dimension to electric guitars. However, it becomes clear that achieving a desired outcome requires a greater understanding of these inherent complexities and how they interact with the recording process, whether in the realm of voice cloning, podcast production, or other forms of audio recording. Ultimately, the utilization of nylon strings on electric guitars necessitates a more profound engagement with sound engineering principles and the specific technical challenges they present.
The Unexpected Challenges of Using Nylon Strings on Electric Guitars A Sound Engineer's Perspective - Unique Composition of Nylon String Sets for Electric Guitars
Nylon string sets for electric guitars offer a distinctive sonic character due to their unique composition. These sets typically feature a combination of wound bass strings and plain treble strings. The bass strings are usually constructed with a nylon or synthetic core wrapped in metal wire, a design that significantly impacts the overall tone. This configuration contributes to the warm, mellow sound often associated with nylon strings, a stark contrast to the brighter, more metallic tone of steel strings.
This distinct sound, while appealing to some, can present a range of challenges, especially concerning tuning and intonation. The inherent lower tension of nylon strings compared to steel strings makes them more susceptible to fluctuations in pitch and necessitates careful setup adjustments. This can lead to difficulties in achieving consistent intonation across the fretboard, potentially affecting the perceived clarity of the instrument's sound.
From a sound production perspective, these features of nylon strings require careful consideration. The softer tone can be challenging to capture accurately with standard magnetic pickups, and their susceptibility to environmental factors like humidity can make achieving a stable, consistent sound during recording sessions a demanding task. Sound engineers might need to adapt their recording and mixing techniques to manage these tonal characteristics and ensure the desired sonic outcomes for audio projects, whether it's voice cloning, podcast creation, or standard music production.
Nylon string sets for electric guitars, while offering a unique sonic palette, present a complex interplay of material and acoustic properties that challenge conventional recording approaches. The core material, often a nylon copolymer, inherently alters the string's vibrational characteristics. Its unique molecular structure differs drastically from steel, leading to a tonal shift towards lower frequencies and a warmer, often mellower, sound. This altered frequency response can pose challenges for sound engineers accustomed to the brighter characteristics of steel strings, as achieving clarity in higher frequencies can become more complex.
The softer nature of nylon also impacts the overall sound, influencing the string's harmonic content. While it can dampen unwanted overtones, potentially resulting in a cleaner sound, this damping can also reduce the brightness and overall attack some genres rely on. Furthermore, the softer material and lower tension inherently reduce the string's interaction with the guitar's magnetic pickups, often resulting in a weaker electrical signal. This weaker signal can make it harder to capture the full dynamic range and clarity of the sound.
Adding another layer of complexity is the sensitivity of nylon to environmental changes. Humidity and temperature fluctuations can drastically impact the string's acoustic properties, leading to unpredictable alterations in pitch and tone. This sensitivity creates a significant challenge in recording, as consistent climate control becomes essential to maintain consistent sound throughout a session.
Intonation can be a real struggle with nylon strings. Their lower tensile strength contributes to greater pitch variations across the fretboard, especially when using alternate tunings. The stability of pitch with nylon is a constant issue for those who attempt to record and manipulate the sounds later with software. These variations require precise adjustments to both the nut and saddle height to achieve the desired intonation across the entire fretboard. The change in the acoustic characteristics and material can also affect the way the sound is captured by the microphones, demanding a reassessment of microphone placement and types to ensure fidelity during recordings.
The inherent flexibility of nylon strings also alters the instrument's dynamic response. It affects how musical dynamics, such as a pianissimo versus fortissimo passage, are captured and translated to the recording. This softer feel can make it challenging to maintain volume consistency, potentially impacting the final mix, especially in genres demanding precise volume control and rapid transitions.
While nylon strings can undoubtedly deliver a unique, warm, and mellow sound, which can be advantageous for certain musical styles like classical or jazz, their application across all genres can be challenging. Heavier styles might find that the reduced attack and sustain from nylon strings fail to deliver the desired brightness and intensity. This highlights the necessity of careful consideration when applying nylon strings to projects with varied tonal expectations.
In conclusion, the use of nylon strings on electric guitars introduces a set of intricate considerations for sound engineers, particularly those involved in the intricate realms of voice cloning, podcast production, or music recording. The unique sonic characteristics they offer are undeniable, but achieving desired results requires meticulous planning, awareness of the material and acoustic implications, and a greater understanding of how these variables interact with the recording process.
The Unexpected Challenges of Using Nylon Strings on Electric Guitars A Sound Engineer's Perspective - Cordoba Stage A Fusion of Traditional and Modern Guitar Design
The Cordoba Stage guitar is an intriguing example of how traditional and modern guitar design can be combined effectively. It features a unique "Fusion Neck" designed for comfort with a 48mm nut width and a faster 16" radius fretboard. This design makes the guitar easier to play, particularly for guitarists transitioning from steel-string or electric guitars. The cutaway body offers enhanced access to higher frets, adding to its overall ease of playability. The guitar's body is a thinline, chambered mahogany with a spruce top and maple veneer, which provides a pleasing visual appearance and contributes to the sound's projection. The integrated EQ system allows players to fine-tune their sound, giving them flexibility in shaping the tonal output, which can be helpful in different performance scenarios like live shows or studio recordings. Yet, there have been some reports of quality control issues such as uneven fret tops. These highlight the challenges of balancing tradition and innovation when crafting new instruments. It appears that maintaining high manufacturing standards is essential for the continued success of this guitar's concept, which bridges the gap between classic nylon-string designs and more modern guitar styles.
The Unexpected Challenges of Using Nylon Strings on Electric Guitars A Sound Engineer's Perspective - Finding the Sweet Spot in Nut Width for Nylon String Electrics
Finding the right nut width for nylon string electric guitars is crucial for both comfort and sound. A common nut width for nylon string guitars is about 1.875 inches, but this may not be ideal for everyone, especially players used to the narrower nuts on steel-string instruments. A narrower nut can be much more comfortable, making it easier to reach across the strings and leading to a smoother, more effortless playing style. Conversely, some players accustomed to classical guitars may prefer a wider nut and string spacing to maintain a more traditional feel. This highlights a tension between playability and classic design elements. This decision is important for sound engineers, as the nut width impacts the guitar's overall tone and how it interacts with recording equipment during audio production—be it voice cloning, audiobook work, or podcasts. The way the strings are spaced on the neck affects the overall sound of the guitar, and therefore it is critical to have a correct nut width to get optimal sound quality.
The interplay between nut width and nylon strings on electric guitars is a fascinating aspect of this unconventional pairing. A wider nut provides more space for fingers, potentially improving accuracy and reducing the chances of unwanted string noise during recording. However, the unique sonic signature of nylon, with its emphasis on lower midrange frequencies, can present mixing challenges. Genres that rely heavily on high frequencies may require more equalization to achieve balance in the final mix.
Magnetic pickups, commonly used on electric guitars, are typically optimized for the stronger magnetic field generated by steel strings. Nylon strings, being less rigid and producing a weaker signal, can necessitate the use of specialized pickups or preamplifiers to ensure a faithful recording of the instrument's nuances. This is particularly important for sound engineers aiming for a detailed audio capture.
Nylon strings, due to their inherent flexibility, exhibit a reduced dynamic range compared to steel. This can make it tricky to capture the full spectrum of a player's expression, requiring careful mic placement and gain staging to ensure that the recording accurately reflects the performance. Maintaining consistent audio quality can be further complicated by the inherent sensitivity of nylon to temperature and humidity fluctuations. Nylon strings are particularly susceptible to these environmental factors, demanding meticulous climate control during studio recordings to avoid unwanted pitch shifts and tonal variations.
Intonation can also be a point of concern when using nylon strings. The lower tension makes them more sensitive to adjustments to the nut and saddle, and intonation can be considerably different from steel strings. These variances can hinder the effectiveness of pitch correction software, particularly in genres that prioritize precise harmonic structures. Choosing the right microphone is also crucial for capturing nylon-string sounds. While dynamic microphones might be suitable for many recording scenarios, condenser microphones are often preferred due to their ability to capture the subtle resonance of nylon strings and their complex harmonic details.
The softer attack characteristics of nylon strings can be an advantage for some genres but can lead to a perceived lack of clarity in others, where a sharp, bright attack is desired. This can influence how percussion-heavy elements are recorded, prompting mixing adjustments to compensate. The distinctive harmonic overtones produced by nylon strings can sometimes overshadow the fundamental frequencies. This can require sound engineers to implement filtering or other processing techniques during mixing to ensure the desired tone is clearly articulated.
Ultimately, the integration of nylon strings on electric guitars presents unique sonic challenges that necessitates a deeper understanding of recording techniques. Sound engineers frequently experiment with various microphone placements and types to find the optimal balance and capture the distinct qualities of nylon strings. This adaptation is another element in the unique production workflow associated with using nylon strings on electric guitars, further underscoring the intricate relationship between instrument, player, and engineer.
The Unexpected Challenges of Using Nylon Strings on Electric Guitars A Sound Engineer's Perspective - EQ Techniques for Optimal Nylon String Sound on Electric Guitars
Nylon strings on electric guitars introduce a unique sonic landscape that demands specific EQ approaches. Their lower tension and distinct tonal profile necessitate adjustments that differ from those used with steel strings. One key aspect involves employing a high-pass filter, generally set around 80-100 Hz, to eliminate muddy low-end frequencies that can cloud the sound. Sculpting the low midrange, specifically the 200-500 Hz zone, can then be used to add warmth and body to the overall tone. Meanwhile, manipulating the high mids—around 1-3 kHz—allows for refining the definition and clarity of the instrument, helping it cut through the mix effectively. Furthermore, utilizing dynamic EQ can prove beneficial when tackling issues such as string noise or tonal instability across different playing dynamics. This technique provides a mechanism for stabilizing the guitar's sonic character, maintaining a consistent sound across chord changes and different playing styles. Mastering these nuanced EQ techniques is essential for realizing the full potential of nylon strings on electric guitars, particularly in projects where the subtle details of sound are critical, like voice cloning or podcast production, where clarity and a nuanced sonic landscape are essential.
Nylon strings, in contrast to their steel counterparts, exhibit a noticeably different sonic character due to their composition and flexibility. This difference manifests primarily in their frequency response, with a tendency towards a more prominent lower midrange. Consequently, sound engineers need to employ specific EQ strategies to avoid a muddy sound and extract the desired clarity and tonal nuances from the recordings. This often involves carefully sculpting the low-mid frequencies, potentially around the 200-500 Hz range, to balance the overall sound and reveal the subtle details.
The choice of microphones becomes crucial when working with nylon strings. Because of their softer attack and unique harmonic texture, condenser microphones often outperform dynamic microphones. Condenser microphones capture the subtle nuances and rich harmonic details that nylon strings produce more effectively, particularly in voice cloning and other applications where capturing every detail is critical.
Another challenge associated with nylon strings is their greater susceptibility to pitch fluctuations, even during a single performance. This inherent instability complicates the task of both the musician and the engineer. Pitch correction software can be less effective with these unpredictable variations, making it essential to meticulously manage tuning throughout the recording process.
The environment in which nylon strings are used plays a significant role in their tonal characteristics. Changes in temperature and humidity can dramatically affect their properties, leading to unpredictable pitch and tonal variations. This sensitivity necessitates precise climate control in recording environments. Otherwise, maintaining a consistent and desirable sound becomes difficult.
Furthermore, the lower tension and flexibility of nylon strings result in a comparatively narrower dynamic range than steel strings. This affects a player's ability to achieve a wide range of expression. Mic placement and gain staging become paramount for capturing the full range of nuances in the performance, as the natural limitations of the nylon strings can easily get lost without careful engineering considerations.
A common issue arising from lower tension is a heightened propensity for buzzing, especially if the guitar’s setup is not meticulously maintained. For example, worn-out nut slots or poorly-cut fret ends can exacerbate the buzzing. Sound engineers need to be prepared to manage these unwanted tonal elements, and sometimes spend considerable time and effort removing the artifacts during the final mix and mastering.
The use of nylon strings on electric guitars often necessitates some adaptation of conventional recording techniques. This is particularly true when magnetic pickups, commonly found on electric guitars, are employed. Magnetic pickups are traditionally designed for steel strings and are less sensitive to the comparatively weaker output of nylon strings. This often leads to a loss of clarity and detail in the captured sound, and sometimes necessitates the use of specialized pickups or external preamps to provide a more robust signal for the recording process.
Recording techniques need to be adapted because of these limitations. Sound engineers may experiment with different microphone positions and types to capture the desired nuances of the instrument's sound. This search for optimum positions can be highly variable depending on the genre or sound aesthetic desired.
It’s interesting that the softer quality of nylon strings, while dampening undesirable overtones and resulting in a cleaner sound in some instances, can also lead to a loss of brightness or attack in certain situations. This highlights the need for sound engineers to make informed decisions regarding EQ and processing to maintain the overall balance of the audio and achieve the desired sound for the particular recording environment.
Lastly, nylon strings' unique feel can alter the way a musician plays. This altered experience impacts how musical dynamics translate to a recording. This can result in variations that would not be typical for a steel-string recording. It is critical that engineers consider these differences to ensure that the recording is as faithful to the performer's intention as possible. In the case of voice cloning or podcast productions, this is critical to maintaining the tone, style and persona of the individual. This calls for careful monitoring of volume levels and dynamic adjustments during the recording process to achieve consistency and overall coherence.
Nylon strings provide a fresh, unique, and desirable sonic character, however, that unique character presents its own challenges. Recording engineers will need to carefully consider these sonic nuances and adapt their techniques when working with them. This careful attention will lead to achieving a high-quality result in a variety of applications including audio books, podcasts, and especially voice cloning where even the smallest details can be crucial.
More Posts from clonemyvoice.io: